With the development of technology, the application of engineering plastics has been expanded to include automotive, home appliances, aviation, medical care, sports, electronics, construction and other fields. We mainly know about the five major engineering plastics, polyamides (PA), polycarbonates (PC), POM, PPO, PET (PBT / PET) from the aspects of their nature of use and processing points.
ONE, Polyamide PA
1 Basic nature
Proportion: PA6-1.14g / cm³, PA66-1.15g / cm³, PA1010-1.05g / cm³
Molding shrinkage: PA6-0.8-2.5%, PA66-1.5-2.2%
Molding temperature: 220-300 ℃
Drying conditions: 100-110 ℃, 12 hours
2 Material performance
Tough, wear-resistant, oil, water, anti-enzyme bacteria, but big water absorption. Nylon 6 has good elasticity, high impact strength and large water absorption. Nylon 66 is better than Nylon 6 in strength and abrasion resistance. Nylon 610 is similar to Nylon 66, but its absorption is small and its rigidity is low. Nylon 1010 is translucent and absorbs little water , Cold resistance is better.
3 Molding characteristics
1,Higher melting point of crystalline materials, narrow melting temperature range, poor thermal stability, material temperature over 300 degrees, the residence time of more than 30min decomposition. Easier to absorb moisture, to be dry, moisture content shall not exceed 0.3%;
2, Good liquidity, easy to overflow material. Should be self-locking nozzle, and should be heated;
3, Forming shrinkage and shrinkage rate, obvious direction, prone to shrinkage, deformation, etc;
4, The mold temperature by the plastic wall thickness of 20-90 degrees within the selected injection pressure by injection machine type, temperature, plastic shape and size, mold casting system selected molding cycle selected by the plastic wall thickness. Resin viscosity is small, injection, cooling time should be taken long, and with white oil as a release agent;
5, Mold casting system in the form and size, increase the size of the runner and gate can reduce shrinkage.
4 The scope of application
Production of general mechanical parts, wear-resistant wear-resistant parts, transmission parts, and chemical, electrical, instrumentation.
TWO, Polycarbonate PC
1 Basic nature
Specific gravity: 1.18-1.20g / cm³
Molding shrinkage: 0.5-0.8%
Molding temperature: 230-320 ℃
Drying conditions: 110-120 ℃, 8 hours
2 Material performance
High impact strength, good dimensional stability, colorless and transparent, good coloring, electrical insulation, corrosion resistance, wear resistance, but poor self-lubricating, stress cracking tendency, high temperature easily hydrolyzed, poor compatibility with other resins .
3 Molding characteristics
1, Amorphous material, thermal stability, forming a wide temperature range, poor liquidity. Moisture is small, but sensitive to water, to be dried. Molding shrinkage is small, prone to melt cracking and stress concentration, it should be strictly controlled molding conditions, plastic parts subject to annealing treatment;
2, High melting temperature, high viscosity, more than 200g plastic parts should be heated extension nozzle;
3, Cooling speed, mold casting system to rough, short principle, should be set cold feed well, the gate should be large, the mold should be heated;
4, The material temperature is too low will result in lack of material, plastic parts matte, the material temperature is too easy to Yi Bian, plastic foam. Mold temperature low shrinkage, elongation, high impact strength, bending, compression, tensile strength is low. Mold temperature is more than 120 degrees when the slow cooling plastic, easy deformation sticky mold.
4 The scope of application
Production of small instruments, transparent insulating parts and impact-resistant parts.
THREE, Thermoplastic polyester
1 Basic nature
As engineering plastics used in PBT unmodified and modified two, unmodified grade molding shrinkage, mechanical properties less than other engineering plastics, it is rarely used alone. Nearly 80% of PBT are modified.
2 Material performance
1, As a milky white crystalline solid, odorless, non-toxic, shiny products surface. Flexibility better than PET, the melting temperature and rigidity are relatively small;
2, With excellent electrical insulation. Even in humid and harsh environments can be maintained;
3, Better weatherability;
4, To resist the corrosion of general chemicals, such as weak acid.
3 The scope of application
1, Making all kinds of car parts, such as door handles, bumpers, mirrors shell;
2, Making electronic and electrical parts, such as connectors, sockets, plugs, fuse boxes, etc .;
3, Producing all kinds of electrical enclosures and components, such as telephone, indoor and outdoor lighting appliances shell, hair dryer components.
1 Basic nature
Formerly used as a fiber, that is, polyester fiber, now the rapid development of engineering plastics, packaging plastics. According to different uses, PET can be divided into fiber grade, film grade, blowing grade and enhanced.
2 Material performance
1, Colorless and transparent or milky white translucent solid;
2, High tensile strength, stiffness and hardness, but has some flexibility, good wear resistance, creep resistance, and can maintain these good mechanical properties in a wide temperature range;
3, With excellent electrical insulation;
4, With excellent weatherability, outdoor exposure in six years, its mechanical properties can still maintain the initial 80%;
5, Resistant to weak acid, organic solvents and oils have good chemical stability.
3 The scope of application
1, Film production, photosensitive film, such as film-based film, fujifilm film camera;
2,As the packaging of food, medicine, textiles, precision instruments, electrical components and other packaging, its production of hollow containers of high strength, good transparency, non-toxic and tasteless, carbonated drinks, beer, edible oil and other widely used plastic packaging materials; electrical material;
3, Used to produce all kinds of electrical insulation materials, such as wires, switches, electrical enclosures.
FOUR,POM
1 Basic nature
Specific gravity: 1.41-1.43g / cm³
Molding shrinkage: 1.2-3.0%
Molding temperature: 170-200 ℃
Drying conditions: 80-90 ° C, 2 hours
2 Material performance
Good overall performance, high strength, high rigidity, good abrasion resistance, low water absorption, good dimensional stability, but poor thermal stability, easy to burn and easy to burn in the atmosphere.
3 Molding characteristics
1, Crystalline material, the melting range is narrow, melting and solidification fast, the material temperature slightly lower than the melting temperature crystallization occurs. Medium liquidity. Small moisture absorption, without drying;
2, Low coefficient of friction, good elasticity, easy to produce plastic surface wrinkles pattern surface defects;
3, Easily decomposed, decomposition temperature is 240 degrees. Disintegration of irritating and corrosive gases. Therefore, the mold steel should be made of corrosion-resistant materials.
4 The scope of application
Production of wear-resistant wear parts, transmission parts, and chemical, instrumentation and other parts.
FIVE,PPO
1 Basic nature
Specific gravity: 1.07g / cm³
Molding shrinkage: 0.3-0.8%
Molding temperature: 260-290 ℃
Drying conditions: 130 ° C, 4 hours
2 Material performance
1, White particles. Comprehensive performance is good, can be used in 120 degrees steam, good electrical insulation, water absorption, but there is stress cracking tendency. Modified polyphenylene ether to eliminate stress cracking;
2, With outstanding electrical insulation and water resistance, good dimensional stability. Its dielectric properties of plastic first place;
3, MPPO for PPO and HIPS blend of modified materials, the current market of materials are such materials;
4, A higher heat resistance, the glass transition temperature of 211 degrees, the melting point of 268 degrees, to 330 degrees decomposition tendency, the higher the content of PPO, the better heat resistance, heat distortion temperature up to 190 degrees;
5, Good flame retardancy, with self-interest, mixed with HIPS with moderate flammability. Light weight, non-toxic for the food and drug industries. Lightfastness is poor, long-term use in the sun will change color;
6, With ABS, HDPE, PPS, PA, HIPS, glass fiber blending modification.
3 Molding characteristics
1, Non-crystalline material, small moisture absorption;
2, Poor liquidity, similar to Newtonian fluid, viscosity is more sensitive to temperature, product thickness is generally above 0.8mm. Easily decomposed, decomposition of corrosive gases. Should be strictly controlled molding temperature, the mold should be heated, the casting system should be small flow resistance;
3, Polyphenylene ether low water absorption rate of about 0.06%, but the trace amount of water will cause the product surface silver and other non-smooth phenomenon, it is best for drying, the temperature can not be higher than 150 degrees, otherwise the color will change;
4, The polyphenylene ether molding temperature is 280-330 degrees, the molding temperature of the modified polyphenylene ether is 260-285 degrees.
4 The scope of application
Made of heat-resistant parts, insulating parts, anti-wear wear parts, transmission parts, medical and electronic components; can be used for higher temperatures gears, blades, valves and other parts, can be used instead of stainless steel; Parts and connectors; motor, rotor, chassis, transformer electrical parts.
Related reading:Nylon Thermoforming Film,PA Base Film,Packaging Films Manufacturer.
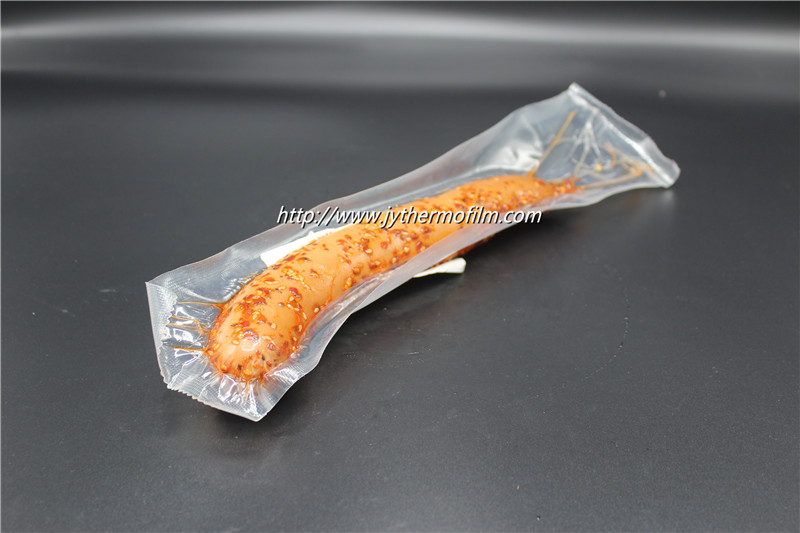